Product overview
IMB-003 BINDER is a screen printing binder that makes a design printed sheet adhere to injection molding resins during insert molding. In particular, it adheres strongly to injection molding resins such as ABS or acrylic resins.
- Solvent type ink
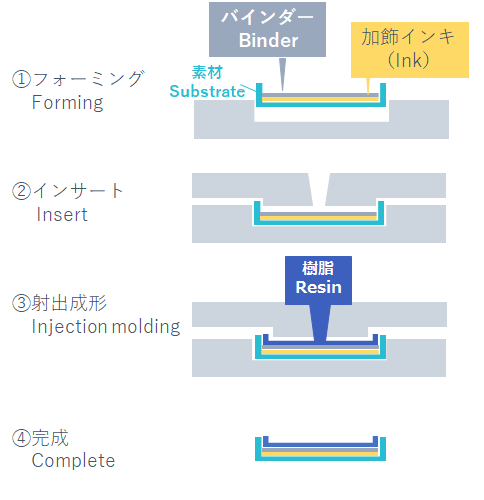
Application
- Adhesive layer for FIM(film insert molding)
- Resin adaptive to injection molding: PC (polycarbonate), PC/ABS、ABS、AS、PMMA(acrylic)
-
Automobile, Motorcycle
-
Home Appliance (IoT)
-
Smartphone, Tablet, Smart watch
-
Sensor
-
Game
-
Others
Features, Function
- Adhesive layer between a design printed sheet on PC sheet or treated PET film with 2 pack curable ink and injection molding resin.
- Excellent adhesion to general purpose resins such as ABS and PMMA resin.
- As screen printing is possible, pattern coating can be applied to only necessary areas.
Substrate
- PC sheet, Easy adhesion treated PET film
- PC
- Easy adhesion treated PET
Dilution
- Dilution is not required.
- *Stir well before use and print only after it becomes fluid.
- *If dilution is necessary, use following solvents. F-002 SOLVENT (standard) F-003 SOLVENT (slow) Dilution 0 to 10%
Recommended cleaner
- Screen Cleaner L2
Mesh
- T 200 to 250 mesh(Coverage would be 30 to 35m2/kg at 200 mesh)
Drying
- Final drying should be performed in accordance with the final drying and curing conditions for design printing inks.
Caution
- Ink should be chosen depending on the printing material and the molding condition, etc.
- Selection should be made based on printing material, molding conditions, etc. Use our IPX and INQ inks for PC sheets and treated PET films.
- When printing a binder, if the underlayer ink is excessively dry, peeling strength will be reduced. Be sure to print continuously up to the binder and conduct final drying.
- In the forming process such as vacuum forming, pressure air forming, and mold forming, as well as in insert molding processes that integrate injection molded resin, a complex set of factors affect the performance of the final product, including the selection of printing materials and inks for design printing, printing conditions, printing sequence, drying method and conditions, selection of molding resin, mold design (gate shape, type and position, number of gates), and conditions set during injection molding.
- Preliminary testing under actual conditions is strongly recommended before a commercial run.
- Binder cannot be used by mixing with screen ink.
- Ink shelf life: 24 months from production date, unopened
Safety
- UN No.: 1210
- UN Classification: Class 3 Flammable Liquids(Flash point is over 23 Degree C)
Handling
- Use safety gloves and eyeglasses to protect skin and eyes. If the ink comes in contact with skin, wash with soap and plenty of water (or lukewarm water) and consult with a doctor.
- Containers should be closed tightly after use and stored in a cool and dark place.
- SDS is available upon request. Please request a copy and read it carefully before handling the products.
Resistance
Formability adhesion test
-
- Test Method
Printed materials of IPX ink and IMB binder made under the following conditions are inserted into a mold for injection molding, and ABS resin is injected onto the binder printed surface for insert molding under the following conditions.
- Test Method
-
- njection molding conditions
Mold clamping pressure :60ton
Mold temperature:60℃
Mold resin:ABS (made by Techno Polymer, 21)
Molded resin temperature :250℃
Injection speed:60mm/sec
Molded item dimension (LxWxH):60×80×2mm - Cut a 1.0 cm-wide slit in the printed sheet side of the test piece, peel it off from the molded resin, and measure the 180° peel adhesive strength (kgf/cm) at a pulling speed of 300 mm/min in a tensile testing machine.
- njection molding conditions
Test results of formability adhesion test (ABS Resin molding)
Tested ink | Tested Binder | 180 °peel adhesion strength |
---|---|---|
IPX-971 Black | IMB-009 Binder | 1.6~2.8 kgf/cm |
IMB-003 Binder | 5.9~6.5 kgf/cm |
-
- Test conditions (Ink)
【IPX- 971 Black】 【F-003 Solvent 10%】 【240 Catalyst 10%】【80℃ 5 min】 【T 250】【Substrate:PC】
- Test condition (Binder)
【IMB-003 Binder, IMB-009 Binder】 【No dilution】 【90℃ 60 min】【T 250】 -
Above resistance test results are measured results in our laboratory and they are not guaranteed values.
- Information contained in this catalog may change without prior notice.
- Test conditions (Ink)
FAQ
-
What is a binder?
-
It is a binding layer, which enhances the binding between the injected resin and the inserted print matter, principally printed with 2 pots of curing ink.
We recommend reading the following reports:
IMB-HF006 Binder (Halogen Free, Environmentally Friendly Binder for IMD/FIM) -
Does ISX Ink need a binder?
-
No, it does not need a binder because ISX ink is a one-pot ink and has good adhesion to injected resin.
-
Why do two-pot inks need a Binder?
-
When cured, a two-pot ink layer has a cross-linked structure and good heat resistance, in other words it is hard to melt at the high temperature of the injected melt resin. Therefore it has inferior adhesion to injected resin. The binder layer between the pattern printed layer and injected resin can strengthen the adhesion between them.
At the time of printing Binder, excessive drying of under layer ink may cause decrease of peeling strength. Be sure to print continuously until Binder before final drying.
- Related technical information
- Related inks