Product overview
VK Ink was developed as ink for automobiles, motorcycles, and outdoor-marking films. The standard colors have excellent weather resistance, and intended resistance can be obtained by using overcoat clear in combination.
- Solvent type ink
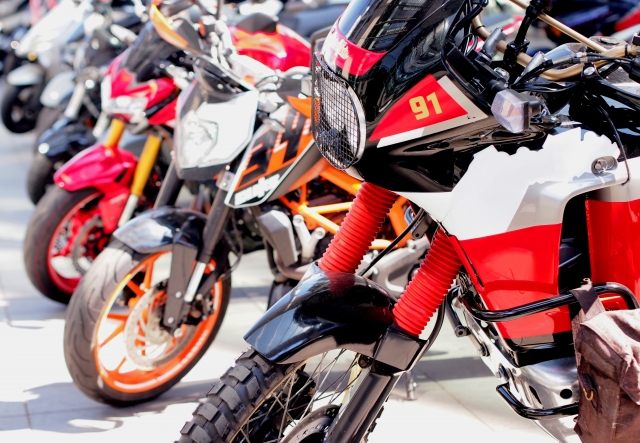
Application
- Automobiles, motorcycles, and outdoor-marking films
-
Automobile, Motorcycle
-
Home Appliance (IoT)
-
Smartphone, Tablet, Smart watch
-
Sensor
-
Game
-
Others
Features, Function
- Standard colors with excellent weather resistance are available.
- Excellent printability and suitable for high-speed printing.
- Multi color setting
- Gloss, Matte
- UV Resistance
- Fast dry, slow dry
Substrate
- PVC stickers, polycarbonate, ABS
- PC
- PVC
- ABS
Dilution
- J-001 SOLVENT(fast) J-002 SOLVENT(standard) J-003 SOLVENT(slow) J-004 SOLVENT(extra slow)
- Dilution: 5 to 25%
- *Z-603 Solvent can be used as a thinning solvent, but the solvent may residue on the sheet. Please be sure to dry thoroughly.
- *Do not use other solvents as they may adversely affect curing, adhesion, stencil stability, or other properties.
Promoter
- SM-90 DEFOAMER 2% (For anti-foam and improvement in leveling)
Recommended cleaner
- Screen Cleaner L2 or J-002 SOLVENT
Mesh
- T 180 to 270 mesh(Coverage is 25 to 35m2/kg at 200 mesh)
Drying
- Natural drying 60 min or more
Each layer 90-100℃ 1 to 2 min
Final layer 50-60℃ 30 min or more
- *Drying time may varies depending on the substrate.
- *It is necessary to know the capacity of the dryer being used and set the drying temperature and time appropriate for the desired printed material.
Standard colors
-
000 MEDIUM
-
001 VICTORIA
-
166 RED
-
168 SCARLET
-
177 OPAQUE RED
-
190 BRIGHT RED
-
242 REDDISH YELLOW
-
246 LIGHT YELLOW
-
247 LIGHT YELLOW
-
277 OPAQUE REDDISH YELLOW
-
391 BLUE
-
516 ORANGE
-
535 ORANGE
-
581 MAGENTA
-
611 WHITE
-
611 C OPAQUE WHITE
-
797 GREEN
-
821 VIOLET
-
911 BLACK
- *The following overcoat clears are available, use according to your purpose. Printing with T 180 to 225 mesh is recommended. Please refer to product information sheet for each clear. SP-3100AU CLEAR: Gloss clear with excellent resistance and weather resistance. SP-4500AU CLEAR: Fast drying gloss clear with excellent weather resistance and scratch resistance.
- *Transparent color (MK) settings for color separation (TC) are also available.
Caution
- Adhesion test must be done before printing as quality of PVC sheet may differ depending on manufacturers or lots.
- Adhesion failure may occur if the release agent is adhered to, or if the material has plasticizers or additives floating on it. It is recommended to wipe the surface of the printed area with alcohol, etc.
- Checking before production: Adhesion and resistance properties may change due to differences in substrates, processes, printing and drying conditions. Be sure to check the adhesiveness and resistance properties before mass production printing.
- Ink shelf life: 24 months from production date, unopened.
Safety
- UN No.: 1210
- UN Classification: Class 3 Flammable Liquids (Flash point is over 23 Degree C)
Handling
- Use safety gloves and eyeglasses to protect skin and eyes. If the ink comes in contact with skin, wash with soap and plenty of water (or lukewarm water) and consult with a doctor.
- Containers should be closed tightly after use and stored in a cool and dark place.
- SDS is available upon request. Please request a copy and read it carefully before handling the products.
Resistance
Test item | Test Conditions | Test results |
---|---|---|
Adhesion | JIS K 5600-5-6:ISO2409(cross-cut), 1mm interval 6×6, cellophane tape and peel | 0(no peel) |
Water | Soak 168 hrs. in tap water, check appearance and peel off | No defect |
Alcohol | Gakushin scrub tester, cotton soaked ethyl alcohol, weight 200g, 500 back and forth, check peel off | No defect |
Scrub | Gakushin scrub tester, cotton, weight 200g, 500 back and forth, check color fade | No defect |
Bending | JIS K 5600-5-1 ISO 1519(Cylindrical Mandrel)2mmΦ, check cracks | No defect |
Humidity and cool-heat cycling test | JIS K 5600-7-4 80℃(4.5Hrs)~-30℃(4Hrs)~50℃95%RH(14Hrs)~25℃(30 min) 3 cycles, check appearance and peel off | No defect |
Accelerated weathering | JIS K 5600-7-7 ISO 11341 Radiant energyー60W/m2、BP Temp.63±3℃ Raining rate18 min/120 min,2000 hrs., check color fade and peel off | No defect |
Test Condition
- Test conditions 【VK-911 Black】 【J-002 Solvent 20%】 【50℃ 10 min】 【T 250】 【Substrate: PVC sticker and polycarbonate】
- Above weathering test was conducted on a PVC sticker with an overcoat of SP-62AU CLEAR.
- Above test was conducted after leaving above printed materials for 168 hours at a room temperature.
- Above resistance test results are measured results in our laboratory and they are not guaranteed values.
- Information contained in this catalog may change without prior notice.
FAQ
-
What is screen printing?
-
Screen printing is a type of stencil printing which uses a technique of duplicating the image from a design made on mesh stencils.
When printing ink goes through the mesh, it transfers the image onto the substrate material. Other than air and water, any substrate materials are printable. Not only flat surfaces, but also curved, specially shaped, and molded products are suitable for screen printing.
-
When over-printed with a black ink, we often have pinholes. How can we eliminate the pinholes?
-
See the list below for causes of pinholes:
1. The first layer is too thin (less than 5 µ)
2. Too much dilution of the ink (more than 20%)
3. Too much squeegee pressure
4. Under layer is pale colored, such as a medium based color
5. Any combination of these causes -
What are the standard drying conditions?
-
In multi-color printing, primary drying would be done after each color is printed. After the final color is printed, the final drying should be done according to the conditions listed in the catalog. If the color printed ink is a “two-pot” ink the final drying should be done after the printing of the Binder.
-
Why there is “Primary” drying and “Final” drying?
-
Residual solvent at the time of injection may cause ink flow and insufficient adhesion. To prevent these malfunctions, residual solvent must be evaporated through a “Final” drying process.
-
When we extended the primary drying time, pinholes and cracks resulted. How can we eliminate them?
-
With one-pot inks, if the primary drying time is too long, the solvent of second ink penetrates the first color layer and makes pinholes.
With two-pot inks, if the primary drying time is too long, a curing process occurs. Thus when the second color is printed, the first color ink layer wrinkles and looks like cracks. The countermeasure in either case would be to shorten the primary drying time.
- Related technical information
- Related event information